Upon shopping for parts for the 63 Buick skylark, I was disappointed by the popularity of wrong parts that are available for this car. Ultimately, I as a consumer get less, and the seller makes a profit. The aftermarket manufacturers of urethane and polyurethane sway bar bushings do not cater to the original design, instead they make their own with brackets($+$=$$). It forces you to buy them both and they lock in more profit. I recall repeatedly forcing the brackets to compress the wrong sized sway bar bracket bushings. I put my faith in the part being correct, but this was a mistake. Today, I can find youtube videos with people using clamps to compress sway bar bracket bushings. There is some normal compression taken up by the hold down bolts, but not the amount most are manufacturing to be normal to all the viewers.
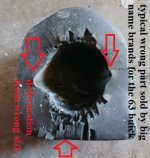
Concern: The wrong parts are sold for the 1963 Buick Skylark.
Correction: Cast sway bar bushings out of urethane in place of worn bushings.
Parts: PMC 790 urethane(Dry Version has no oil), scale, mixing cup, Vaseline, gloves, particle board, wood dowel, and other safety equipment.
PMC™-790 Product Information
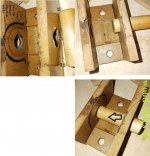
First, remove sway bar brackets, clean and paint brackets and sway bar at points of contact as necessary, allow to cure overnight. Continue to measure sway bar outer diameter with digital caliper. Attain, wood dowel to match diameter and size to sway bar. Also cut out your particle board pieces that will make the mold. Use screws to secure together. Make alignment marks for brackets and test assemble. Coat with tung oil or paint the particle board to prevent moisture contamination which causes bubbles in urethane. Additionally, coat all parts with vaseline before pouring in the PMC790, this will allow for ease of disassembly. Optional, you can form the particle board to make details such as at the base of the bushings with a sanding bit or even a carbide bit.
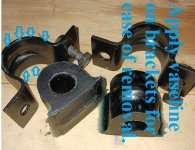
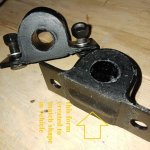
Second, read all documentation for the PMC 790, prior to using it. The 790 will cure as hard as a hard tire. If you want softer PMC 780 will do. PMC 770 will be closer to the so-called rubber bushings you would get in the aftermarket.
Third, pour mix into the mold with brackets secured with hold down sway bar bolts. Make more mix rather than less so that it overflows a bit. Cap and let sit for full cure time. Clean up excess. If you have large bubbles after taking mold apart, you can make a small batch and touch up the cast part. Urethane will bond to itself sooner rather than later. You can cheat and check it before the 24 hour or 48 hour it calls for.
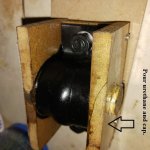
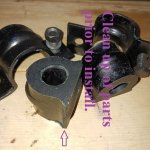
Fourth, after clean-up of flash on cast parts make a cut for ease of installation. Use a very sharp tool, do not use a dull blade this may cause injury. Preferably use leather gloves for added protection. Install on sway bar, apply grease and rotate.
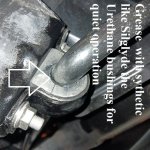
Summary: Some of the methods, I introduced for example Vaseline are for keeping expense down, there is a 200 spray that you can use instead. If you select the hardest durometer with the pmc790, there is less room for compression, so measure two or even three times to get it right. If you want to go on the safer side you could go with PMC780 and have some, compression. As an added test rotate the sway bar with brackets bolted on and without the links and check for snug fit. Should not be loose. If you made it this far than the most obvious is that now you have the most custom-made bushings that fit your sway bar and brackets that no one can match.
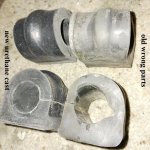
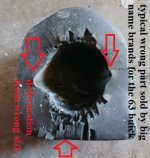
Concern: The wrong parts are sold for the 1963 Buick Skylark.
Correction: Cast sway bar bushings out of urethane in place of worn bushings.
Parts: PMC 790 urethane(Dry Version has no oil), scale, mixing cup, Vaseline, gloves, particle board, wood dowel, and other safety equipment.
PMC™-790 Product Information
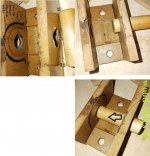
First, remove sway bar brackets, clean and paint brackets and sway bar at points of contact as necessary, allow to cure overnight. Continue to measure sway bar outer diameter with digital caliper. Attain, wood dowel to match diameter and size to sway bar. Also cut out your particle board pieces that will make the mold. Use screws to secure together. Make alignment marks for brackets and test assemble. Coat with tung oil or paint the particle board to prevent moisture contamination which causes bubbles in urethane. Additionally, coat all parts with vaseline before pouring in the PMC790, this will allow for ease of disassembly. Optional, you can form the particle board to make details such as at the base of the bushings with a sanding bit or even a carbide bit.
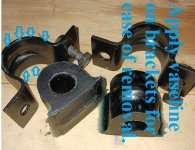
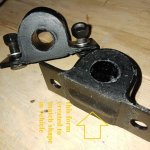
Second, read all documentation for the PMC 790, prior to using it. The 790 will cure as hard as a hard tire. If you want softer PMC 780 will do. PMC 770 will be closer to the so-called rubber bushings you would get in the aftermarket.
Third, pour mix into the mold with brackets secured with hold down sway bar bolts. Make more mix rather than less so that it overflows a bit. Cap and let sit for full cure time. Clean up excess. If you have large bubbles after taking mold apart, you can make a small batch and touch up the cast part. Urethane will bond to itself sooner rather than later. You can cheat and check it before the 24 hour or 48 hour it calls for.
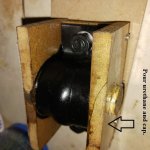
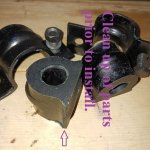
Fourth, after clean-up of flash on cast parts make a cut for ease of installation. Use a very sharp tool, do not use a dull blade this may cause injury. Preferably use leather gloves for added protection. Install on sway bar, apply grease and rotate.
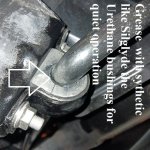
Summary: Some of the methods, I introduced for example Vaseline are for keeping expense down, there is a 200 spray that you can use instead. If you select the hardest durometer with the pmc790, there is less room for compression, so measure two or even three times to get it right. If you want to go on the safer side you could go with PMC780 and have some, compression. As an added test rotate the sway bar with brackets bolted on and without the links and check for snug fit. Should not be loose. If you made it this far than the most obvious is that now you have the most custom-made bushings that fit your sway bar and brackets that no one can match.
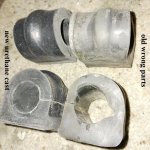
Attachments
Last edited: